Biodiesel is a domestically produced, renewable fuel that can be used in place of petroleum diesel. Use of biodiesel reduces greenhouse gas emissions of carbon dioxide and particulate matter that are associated with major health distress, including cancer.
Biodiesel also reduces hydrocarbon emissions that contribute to the formation of ground level ozone, as well as carbon monoxide, a poisonous gas associated with fuel combustion.
In addition to the reduction of environmental and health threats of the fuel, biodiesel also helps reduce the country's dependence on foreign oil imports.
Yet, agriculture and forestry industries remain reticent to assist these technologies into commercial application because to do so gives rise to much risk. Blends of 20% biodiesel with 80% petroleum diesel (B20), can generally be used in unmodified diesel engines; however, users should consult their OEM and engine warranty statement.
It may require certain engine modifications to avoid maintenance and performance problems and may not be suitable for wintertime use, especially if made from animal fat. And, it only reduces foreign oil by 20%.
It takes about 7.3 pounds of soybean oil, which costs about 20 cents per pound, to produce a gallon of biodiesel. Feedstock costs alone, therefore, are at least $1.50 per gallon ($1.88 as of June 2007) feedstock for soy-based biodiesel. Add in your infrastructure, labor and hauling costs and the per gallon amortizes upward. Compare that with our <$1.50 production costs with low cost, free or even paid for feedstock, the advantage of the HC³ is quite obvious.
Environmental concerns that must be addressed include fugitive emissions of methanol, the ultimate disposal of the by-product glycerin, and the generation and disposal of wastewater containing free fatty acids that have a high biochemical oxygen demand, or BOD, that can remove oxygen from water bodies and harm aquatic life.
Odd factoid:
The conversion of an automobile engine to burn vegetable oil is not legal under US Environmental Protection Agency guidelines. The EPA has not fined anyone for doing so, but certain laws may have to change, or a certification process may need to be established.
Most parameters of biodiesel also apply to Energy Visions diesel, as the HC³ method can also utilize vegetable oils, indeed, any organic substance for processing, They are not our prime target, though.
Biodiesel has become the fuel of choice for environmentally conscious consumers, mainly in Europe; but slowly now also in America. Germany alone, has 1700 gas stations, (about 10%), selling biodiesel.
With a market share of approximately 50% of new cars, and traditionally many passenger diesel vehicles operating in Europe it seems clear that drivers and communities there have made a decisive course correction. Unfortunately, the preponderance of this fuel is still made from raw petroleum crude. However, as the home of the HC³, inroads are being made. Still, it is clear that Europeans have put diesel at the top of their list.
"Biodiesel" is a clear amber-yellow liquid with a viscosity similar to petrodiesel, the industry term for diesel produced from petroleum. However, it is chemically different. Chemically, biodiesel comprises a mix of mono-alkyl esters of long chain fatty acids. The term refers to any diesel-equivalent biofuel derived from renewable materials called F.O.G.; Fats-Oils-Grease, such as vegetable oils or animal fats.
Brown grease, (restaurant greasetrap residue) does not convert well via the transesterification process for biodiesel, but would also be a good feedstock for HC³.
Several different kinds of fuels are called biodiesel, but usually the term "biodiesel" refers to an ester, or an oxygenate, made from any oil and methanol. Sometimes even unrefined vegetable oil is called "biodiesel." This unrefined vegetable oil requires a special engine; leaving the quality of petrochemical diesel higher.
One of the state EPA permit obligation is liability insurance if some fuel is spilled on the ground. The company must show a financial ability to clean it up. Biodiesels are biodegradable and non-toxic.
Biodiesel, plus HC³, can be distributed using today's infrastructure. Many fuel stations are beginning to make biodiesel available to consumers. A growing number of transport fleets use it as an additive in their tanks.
Biodiesel is generally more expensive to purchase than petroleum diesel, while the HC³� is anticipated cheaper; although this differential may diminish due to economies of scale, for example, the rising cost of petroleum, and government subsidies favoring the biodiesel arena.
- Biodiesel does produce more NOx emissions than petrodiesel, but these emissions can be reduced through the use of catalytic� converters. The increase in NOx emissions may also be due to the higher cetane rating of biodiesel. Properly designed and tuned engines may eliminate this increase.
- Biodiesel has higher cetane rating than petrodiesel, and therefore ignites more rapidly when injected into the engine. It also has the highest BTU content of any alternative fuel (except HC³) in its pure form (B100).
- Biodiesel is biodegradable and non-toxic - tests sponsored by the United States Department of Agriculture confirm biodiesel is less� toxic than table salt and bio-degrades as quickly as sugar.
- Biodiesel is the only alternative fuel to have successfully completed the Health Effects Testing requirements of the Clean Air Act (1990).
HOWEVER . . . DIESEL NOT FOR BIODIESEL
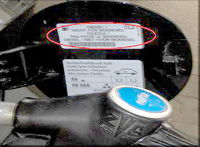
Some car manufacturers, due to the impact on engines, refuse biodiesel. Technically, the down side of oil biodiesel can be somewhat off-putting.
Most disadvantages of biodiesel, on the other hand, do not apply to HC³ technology.
Parameters can be fine-tuned with the proper raw input material mix (example; plastic waste, straw, and animal fat added to vegetable oil; all in ONE process). The wide range of applicable materials that can be used in the HC³ process is therefore a strong advantage.
Worldwide production of vegetable oil and animal fat is not yet sufficient to replace liquid fossil fuel use.
Furthermore, some environmental oversight groups, notably the Natural Resources Defense Council, object to the vast amount of farming and the resulting over-fertilization/pesticide use, as well as the land use conversion that would be needed to produce the additional vegetable oil.
There is also the resultant rape of south Asian rainforests to secure palm oil now that biodiesel has become so popular. The only organic slaughter attributed to the HC³ is the commodity on a trash haul truck.
THERMAL DEPOLYMERIZATION (DIRECT HYDROTHERMAL LIQUEFACTION)
Direct hydrothermal liquefaction involves converting biomass to an oily liquid by contacting the biomass with water at elevated temperatures (300-350°C) with sufficient pressure to maintain the water primarily in the liquid phase (12-20 MPa) for residence times up to 30 minutes. Alkali may be added to promote organic conversion.
The primary product is an organic liquid with reduced oxygen content (about 10%) and the primary byproduct is water containing soluble organic compounds. In a second process step, requiring additional energy, the dewatered refuse is then converted into diesel.
Hydrothermal treatment is based on early work performed by the Bureau of Mines Albany Laboratory in the 1970s. Developers include Changing World Technologies (West Hampstead, NY), processing turkey slaughtr residue from the Little Butterball factory. Turkey bone, containing a zeolitic substance are used in some cases, which has similar effects as the catalyst the HC³ utilizes.
More than 150 zeolite types have been synthesized and 48 naturally occurring zeolites are known. They are identified as basically hydrated alumino-silicate minerals with an open structure that can contain a wide variety of positive ions, such as Na+, K+, Ca2, Mg2 and others.
The is proprietory insofar as it employs an ion exchange process as well, which allows elimination of undesirable side products (heavy metals, chlorin, etc.). Direct Hydrothermal Liquefaction consumes substantially more energy than the HC³, which has a strong influence on the bottom line.
FISCHER-TROPSCH GAS-TO-LIQUIDS
Scientists long have tried to convert natural gas (methane) into liquid fuels. A conversion scheme was worked out in the 1920s by the German chemists Franz Fischer and Hans Tropsch. The Fischer-Tropsch process reacts methane with air over a catalyst to create synthesis gas, a mixture of carbon monoxide and hydrogen. This gas mixture is then converted to a mixture of liquid hydrocarbons using another catalyst. The Fischer-Tropsch product has essentially no sulfur or aromatics.
The Fischer-Tropsch process has not seen wide commercial use because it is expensive and has a negative energy balance. It is receiving new interest lately because of its potential to bring "remote" natural gas to traditional markets. Researchers claim that recent advances make the process economically competitive, and as a result, several major projects are being planned. If the technology proves successful, it will provide a new source of high-quality kerosene, but at high costs.
The Fischer-Tropsch process cannot avoid harmful emissions and has a negative energz balance (require more energy input than the energy contents of the output). It is not are not able to reliably capture hydrocarbon pollutants, such as halogens and/or heavy metal steams, which often remain in the final product of existing facilitites.
Transforming residual substances with recycling procedures based on the Fischer-Tropsch process, requires high pressure and temperatures of 450°C and higher, a temperature at which coke crystals begin to form from residual substances.
Such high temperature procedures decompose the hydrocarbons in the plant nearly completely into coke crystals and methane.
However, while coke and methane can be used further as an energy output, the by-products of such high temperature procedures, like CO2, Dioxin and Furans, are an unacceptable environmental hazard.
PYROLISIS
Pyrolysis is the chemical decomposition of organic materials by heating in the absence of oxygen or any other reagents, except possibly steam. Extreme pyrolysis, that leaves only carbon as the residue, is called carbonization. Pyrolysis is a special case of thermolysis.
Solid biomass can be liquefied by pyrolysis, hydrothermal liquefaction, or other thermochemical technologies. Pyrolysis and gasification are related processes of heating with limited oxygen. Conditions for producing pyrolysis oil are more likely to include virtually no oxygen. Pyrolysis oil or other thermochemically-derived biomass liquids can be used directly as fuel.
Pyrolysis and gasification are related processes of heating with limited oxygen. Conditions for producing pyrolysis oil are more likely to include virtually no oxygen. Pyrolysis oil or other thermochemically-derived biomass liquids can be used directly as fuel.
Fast pyrolysis of biomass produces a liquid product, pyrolysis oil or bio-oil that can be readily stored and transported. Pyrolysis oil is a renewable liquid fuel and can also be used for production of chemicals. Fast pyrolysis has now achieved a commercial success for production of chemicals and is being actively developed for producing liquid fuels. Pyrolysis oil has been successfully tested in engines, turbines and boilers, and been upgraded to high quality hydrocarbon fuels although at a presently unacceptable energetic and financial cost.
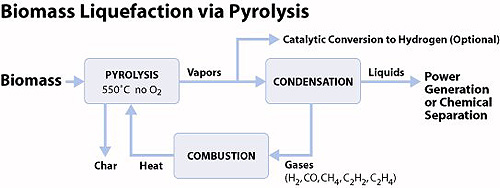
For further details refer to: http://www.eere.energy.gov/biomass/pyrolysis.html
OUR HC³ BIOMASS-TO-FUEL TECHNOLOGY
To be clear, it should be noted, that we are not concerned with the ethanol process. Ethanol is for gasoline; the HC³ technology is strictly diesel—Ultra Low Sulfur Fuel; ULSD The HC³ is quite different from other conversion process currently in progress. While in the same arena, the departure occurs with its source feedstock.
The HC³ process, which Energy Visions employs exclusively, uses mostly undesirable waste material; a substance that is out-distancing our capability to dispose of it. Further, it can utilize the leftover refuse of other methods, agri-growth, plastics, municipal waste, in fact any organic material.
The HC³ unit works under a very slight negative pressure and low tempoeratures, which makes the process extremely energy efficient, using only 10% (!) of the produced energy for production.
The cracking of the large CH-chains are performed by the catalyst, at temperatures around 550° F, with some substances cracking above 600° F. Other methods use mainly higher tempertures and/or pressure, reaching more than 750 psi, which equates to more energy (= cost).
Expert Opinion
Concerning the Industrial Application
Of the HC³ Technology
(Pressure-less Catalytic Deplomerization)
By Request of: Alphakat Zukunftsenergie
Gesellschaft f�r Katalytische Aufbereitungstechnologien mbH
Schulstraße 8, 96155 Buttenheim/Germany
Expert
Dr. Erhard Tschirner
Consulting Services for
Environmental and Industrial Analysis
Melwitzer Weg 16j, 06366 K�then/Germany
May 2006
Fuel produced from biological regrowth material are progressively offering an alternative to the mineral oil production from crude oil, and are crucial for this decentralized, energy-technical future. They have the potential to add to, or replace the insufficient supply of crude oil in the future.
But to replace only a fraction of the vast amount of crude oil production by synthetic fuel production, large volumes of suitable raw material will be necessary. We can find these substances, not only in regrowth raw material like wood and plant (vegetation) waste, but also in the tremendous amount of waste material that our civilization produces. For example plastic, animal and vegetation waste, waste oil and other organic residue, which we will call for simplification, i.e. organic energy-containing substances.
Present recycling methods, like the high-temperature gasification with subsequent Fischer-Tropsch Synthesis—and a total Wirkungsgrad of less than 10%, cannot fulfill this requirement. This is also true for other know processes like the pyrolysis, which in addition to setting free or producing harmful gasses like dioxins, halogens and gaseous heavy metals. These cannot be filtered out by the production plant and enter the final product.
The reasons for this unsatisfactory situation results from deficiencies in the basic structure of the known processes. In all known conventional processes the conversion of OES requires temperatures in excess of 450° C and higher. The conversion as such is achieved by production of coke crystals from the OES that start appearing at temperatures around 400° C. They dissolve the hydrocarbons in the plant unit almost completely into coke crystals and methane.
With this process, the hydrogen from the existing hydrocarbons is converted into methane CH4 and coke crystals (C), which means that the hydrocarbons, which could be converted into fluid form are actually converted into the solid coke and methane gas CH4. Though it is possible to make use of coke and methane, the energy balance is dissatisfactory and harmful substances and the negative influence on the environment by CO2, dioxin, and furanes are intolerable.
Other technologies, based on alternative energy carriers like hydrogen, require large amounts of energy and use of other limited resources, for example platinum, and are still in a very early stage of development.
A crucial element of the HC³ technology, which does not have the disadvantages mentioned, is the newly developed and patented zeolithic high-performance catalyst of the y-type. This catalyst allows it to perform the necessary process in a low temperature range between 530 and 650° F.
The supply is world-wide sufficient.
On a molecular level the following reactions happen:
- The extraction of CO2 resulting in the product CnH2n
- Shortening of the hydrocarbon molecules
Realized requirements of the HC³ process:
- Shredding of solids to a particle size of 5 mm at the thinnest section.
- Utilization of an induction system
- Pre-warming and partly dewatering in preparation for the conversion
- Dissolution of the particles in a self-replenishing carrier oil suspension
- Energy input by a gradient-minimized induction system
(reaction mixer "turbine")
- Providing electrical energy and process heat via a co-generation plant with
heat recycling and a utilization system by use of an ICR reactor.
- Processing and dispatch unit for anorganic residue by extracting extrudable and evaporative hydrocarbons
- Production of usable gas oil by distillation/rectification
The contents of Illustration 2 is based on extensive and reproducible test data, from tests by the University For Applied Technologies in Hamburg, which supports our statements above with quantitative test results in a comparison of various biomass fluidization methods.
Illust. 2� |
Process |
Efficiency* |
Yield gls/acre |
Hu� BTU/lb |
Densitykg/l |
Yield to/acre** |
Costs $/gallon |
Costs $/gal Diesel*** |
Methanol |
40-50% |
530 |
9,071 |
0.8 |
0.80 |
1.63 |
3.49 |
Ethanol |
33-50% |
445 |
11,908 |
0.8 |
0.88 |
2.00 |
3.27 |
RME1) |
45-54% |
170 |
15,906 |
0.9 |
0.52 |
2.50 |
2.72 |
FT Diesel2) |
40-47% |
212 |
18,271 |
0.85 |
0.68 |
3.18 |
3.18 |
HC³ Diesel |
70-75% |
953 |
13,757 |
0.86 |
2.36 |
1.043) |
1.393) |
- RME = Rapeseed-based Biodiesel
- FT Diesel= Fischer-Tropsch method
- For HC³500; costs can be substantially lowered with HC³2000 and larger plants (see sample calculations in the appendix)
*Energy efficiency = (calorific value of product/outside energy for process) calorific value of raw material
**1 t.o.e. (energy equivalent of one metric ton of oil); 1 toe = 41.9 GJ; 16 MBTU/ton
Source: Prof. Dr. Ing. Willner, University for Applied Science, Hamburg
The figures above prove that the HC³ process, as a single-step direct fluidization process, provides the lowest cost (per energy unit) added by the highest comparable energy yield per acre.
Besides the very important utilization of waste material as feedstock, of similar importance is the conversion of biomass to fuel. This is not only of economical but also of political significance, whereas different goals and subsidy policies are followed.
Estimates of the FNR (Fachagentur fuer nachwachsende Rohstoffe; Agency for Regrowth Raw Materials), point out that on one hectare of agricultural land approximately 4000 liters (1050 gal) of BTL fuels can be produced. Under these considerations, in the future about 20-25% of the total fuel consumption in Germany could be replaced, while for Europe in total, the figure is even substantially higher. This means that BTL fuel could substitute for a very significant amount of fossil fuels.
BTL is an acronym for Biomass-to-Liquid and is like GTL (Gas-to-Liquid) and CTL (Coal-to-Liquid) one of the synthetic fuels, which are precisely tailored to the requirements of modern engine concepts. According to Prof. Willner in a lecture in Hamburg, utilizing the HC³ process results in 9000 l/ha�(962 gal/acre). In other words, the share of BTL in replacing fossil fuels in Germany would increase to about 50%. Other countries would experience the same positive effect.
Concerning subsidies for fuels from biological sources (LEIBLEIN 2006, 3), a differentiation is necessary, if the target is the market implementation and market penetration (e.g. for biodiesel and bioethanol), or demonstration, including the feasibility of supply and use of second-generation biofuels (e.g. Fischer-Tropsch-Fuel, HC³ Catalytic Pressure-less Depolymerization and Hydrogen). An evaluation is only possible, if the goal has been clearly defined.
In respect of the explicit support of CO2 reduction, concerning the cos for the CO2reduction, it becomes obvious that production of heat and electricity from biomass has substantial advantages in comparison to the production of Fischer-Tropsch-Fuels. While, for example, the CO2 reduction costs from straw and forest undergrowth with the FT method exceed $250, the conversion into heat does not create any costs nor create even a profit (negative costs). For conversion into electric energy, the respective costs for CO2 reduction are in the range of $50 to $75 per ton CO2.
(The following paragraph deals with political targets and tax laws in Germany and has no relevance for the situation in the US. We have therefore skipped it.)
Fuel produced from biomass via the HC³ process is free of tax.
(Again German tax law)
In total, the industrial scale technological implementation of the HC³ process offers substantial advantages in the market place. We expect a short term or mid term expanding market for:
- Plant equipment (especially steel and tank production)
- Production of electronic control elements
- Customer-specific engineering
- Turbine production
- Catalyst production
- Civil and construction engineering
In the national and international arena, we estimate the potential turnover of $125 million during the start-up phase of three years.
TECHNOLOGICAL DEVELOPMENT OF THE HC³ PROCESS
The following pictures show the history of the scaling process.
Based on the principle configuration of the facility, the centerpiece at this time was still a separate, coupled conveying pump-turbine combination. The material stream is channeled from a separation vessel to the cyclon.
Here the gas oil vapor, produced by the catalytical process is transferred via a condenser to the column for rectification. Solid feedstock is fed by the conveyor screw gear into the separator chamber. Solid residue, including the inactive catalyst, are carried outside and cooled.
Most important results were improvements of material and sealings under high thermal stress as preparation for planned industrial scale online service.
In parallel, a HC³500 unit (capacity of 500 liters of gas oil per hour) was built in Mexico and was prepared in test runs for the industrial application. The purpose of the unit was the conversion of heavy oils containing chlorine from the stream of special waste to a medium distillate in the range of diesel components.
The energy induction system used in this case is based on friction heating system, known from nuclear poser plants, and a friction flow reaction for the low temperature conversion unit (600° to 650° F).
(Comment: The pumps have been recently replaced with the latest turbine system patented in March 2006, which provides the necessary�dwell time for the feedstock-catalyst mixture of 3 minutes, more efficient and with less wear and tear.)
At the end of 2005 and beginning of 2006, based on the previous development work, production of the patented turbine (high-performance encapsulated chamber mixer) was introduced and implemented thereafter. It allows an effective mixing process of the catalytic oil suspension. It works as a reactor for depolymerization and polymerization of hydrocarbon containing waste material, into middle distillate (diesel) in a circuit.
This unit has been fully tested and is applied on an industrial scale as a 30kw, high performance, encapsulated chamber mixer for various types of feedstock for direct oil conversion.
The most important technological progress of this invention is the replacement of the heat induction from the outside of a vessel, which always requires higher temperatures than the inside material is subjected to, and reaches the catalytic process temperature of the HC³ technology with less energy input.
Utilizing this technological set-up, the following results from 1t (metric) of feedstock have been achieved, utilizing rapeseed (canola) press cake:
Feedstock |
TS(%) |
Ashes(%) |
Orig. Matrix (%) |
Loss of mass |
Diesel (kg) |
Diesel (gal) |
Press cake |
88.6 |
7.7 |
76.0 |
31.2 |
296 |
93.4 |
Canola oil |
99.9 |
0.3 |
99.6 |
1.0 |
291 |
91.8 |
Sum |
|
|
|
|
587 |
185.2 |
The successful finalized tests with the HC³ 500, also provided important data for the further process development of the HC³ 500 technology. The graphs show a schematic overview of the development status of the machinery technology, which is now ready for industrial application.
The development was performed by Alphakat's OEM partner, DSD GmbH Gommern, for an order from a Canadian customer in the field of electronic waste recycling. It contains all-important design elements provided by Alphakat Engineering GmbH, Remscheid, for the technical process flow of HC³ units of this size class.
In the field of small and mobile HC³ plant design and technology, the specialized companies are Alphakat Zukunftsenergie Gesellschaft Katalytische Aufbereitungstechnologien mbH, Buttenheim - Zukunftsenergie Floetz GmbH. - Alphaka GmbH production facility Eppendorf and the Alpha Mobile Power GmbH, Markt Bibart; all are working in the national and international marketplace.
Turnover is generated by planning and construction of prototypes, modules and parts for HC³ units, as well as complete facilities in the sizes mentioned above, for research and industrial applications of residue and regrowth feedstock processing.
Customer-specific service sector for project preparation as well as an after sales service, which is under development, also provide important input with respect to expansion in the fields of busines administration and personnel.
In addition to the vast amounts of raw material, a high efficiency for processing is necessary, or in other words, the hydrocarbon material contained in the OES, should be converted as far as possible, and with as little as possible residual substances, into commercial grade fuel.
Dr. Erhard Tschirner
Environmental and Industrial Analysis
It is essentially a mechanical and not chemical process, as is HC³.
HC³ utilizes, with various additives, the feature of zeolites in providing a "mesh effect" or lattice structure. Long CH chains do not fit into this lattice structure and are thus, with the help of a moderate heat, broken up into shorter chains or diesel fumes; later distilled to hi-grade, ultra-low sulfur diesel.
This is a proprietary technology, no one else can provide.
In other methods, there seems to be similar or the same advantages as HC³:
-
It is highly effective at killing pathogens, specifically those including
prions, which is crucial, for example, in foul, beef, and other meat
processing plants.
- It can also safely remove heavy metals from the samples by
converting them from their ionized or organometallic forms,
to their stable oxides; in the case of HC³ (salts) which can then
be safely separated from the other "value added" products,
such as the pure diesel and distilled water.
In comparison to the HC³,
pyrolisis and other waste-to-fuel processes have two disadvantages, effecting costs:
The significant higher pressure requires additional energy input, thus the net energy balance is by farnot as high as the HC³ achieves.
- As the pyrolysis processor has to work under a high pressure of 750 psi, the machinery has to be built to pressure vessel standards, which means it has to fulfill all the regulations that a typical refinery for fossil fuels
would require. Operational risks and costs are therefore�higher. �
This means higher construction costs, more sophisticated safety
devices and higher insurance expenditures than the HC³ requires.
- A leak in one of the pressurized vessels would free large amounts
of dioxins into the atmosphere. (The HC³ runs at a slight negative).
This means higher temperature/higher pressure systems have to fight with the same solid carbon problems as Fisher-Tropsch and "pure" Pyrolisis. For example, with the use of surface heating, they produce elemental carbon, which is difficult to separate and scums the production facility.
With certain feedstocks containing chlorine, they will produce dioxins and furans, which limits the scope of application.