Comparison
THE STRONG POINTS
Where CC sparkles.
Amazingly, CC is different from ethanol and biodiesel, which are—even with upcoming technologies—restricted to plant matter, i.e. sugar, starch, and vegetable oil.
This technology can in addition, utilize Anya organic matter, from waste oil to farm chaff to industrial refuse and household garbage, to food industry residue and slag, discarded computer carcasses, disaster clean up (including oil spills), and non-recyclable plastic (86% of all PET bottles end in landfills! Most of the rest is exported overseas).
Actually, in shipping, we can take bilge oil and return it as ultra-low sulfur diesel.
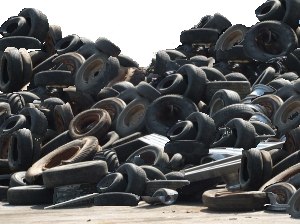
The CC (catalytic conversion) process can even improve the yield from crude oil in conventional refineries by up to 20%, as it is able to convert residue like tar or bitumen into high-grade diesel fuel, such as in the Mexico facility.
The efficiency of CC diesel is substantially higher than that of other alternative fuel.
- The volumetric yield, gallons per acre, for example, is double that of ethanol and up to five times that of biodiesel.
- The energy yield per acre is four times that of ethanol and almost five times that of biodiesel (from canola).